5 Questions to Ask when You’re Serious about Improving Fuel Efficiency
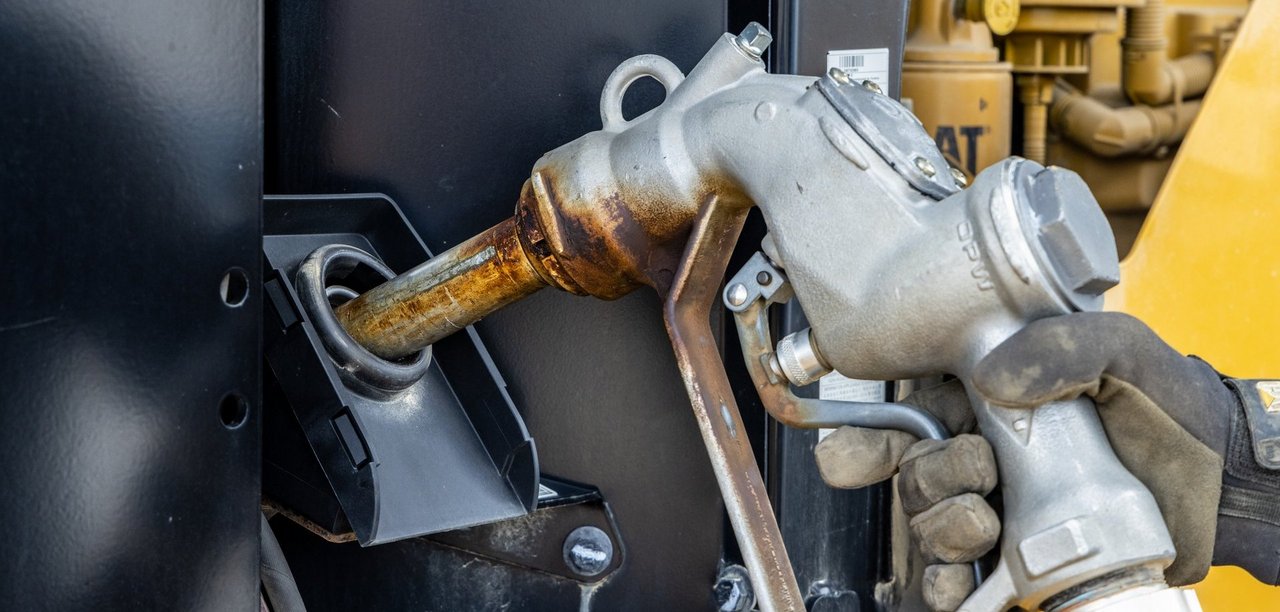
No matter what you’re paying for fuel these days, it’s a huge cost driver. To manage that cost, you’re challenged to use fuel efficiently. In other words, you want to do as much work as you possibly can with every tank you buy and burn. There’s no simple way to improve fuel efficiency, but if you’re up the job, here are five questions to consider.
1. DO WE HAVE THE RIGHT EQUIPMENT?
—
If your highly utilized machines are showing their age, it could be tough to improve fuel efficiency. Newer models are more apt to be equipped with powertrain components that are optimized for peak efficiency. They’re also more likely to include fuel-saving features and technologies—like automatic engine idle shutdown and economy mode or grade control and payload management systems. As you think about upgrading key machines, be sure to consider sizing, system matchup, blade or bucket choice and GET selection. They all affect fuel efficiency.
2. IS THE SITE SET UP TO MAXIMIZE FUEL EFFICIENCY?
—
The right workflow can produce big gains in productivity and fuel economy. To spot inefficiencies on your site, look carefully at job setup. Are the loading and hauling machines sized right? Do they function as a system? Is work being completed in short, consistent cycles? How many machines are idling and why? Are travel routes direct, short, straight and clear of obstacles? There’s a lot to consider when evaluating site setup. Getting an efficiency expert involved can be a good move.
3. ARE WE USING THE DATA?
—
The easiest and most accurate way to track and improve fuel efficiency is with telematics data. It provides a precise measure of fuel consumption, idle time, production time and equipment utilization. It can help you identify machines that burn too much fuel or operators who need extra training. Manual methods can be used to capture fuel data, but a telematics system provides the information quickly, accurately and automatically.
4. ARE OPERATORS GETTING THE RIGHT TRAINING?
—
Operator technique plays a big role in fuel efficiency. That’s why it pays to teach fuel-saving operating techniques to all who run the equipment. Focus on consistent operation—fewer big swings in acceleration and deceleration. Communicate the importance of reducing idle time. And coach them to use the various operating modes to balance productivity and efficiency.
5. IS MAINTENANCE DONE ON TIME AND TO SPEC?
—
Keeping equipment well-maintained goes a long way toward improving fuel efficiency. Stay on top of daily tasks like greasing components, adjusting belts, inflating tires and inspecting track. Plan preventive maintenance using telematics data and other condition monitoring information. And execute the plan as scheduled to keep the fleet performing efficiently and reduce the risk of unplanned failure.
For more information please contact US:
Estonia +372 679 9260 | info.ee@avesco-cat.com | Latvia +371 2 570 17 11 | info.lv@avesco-cat.com | Lithuania +370 52 603 242 | info.lt@avesco-cat.com |